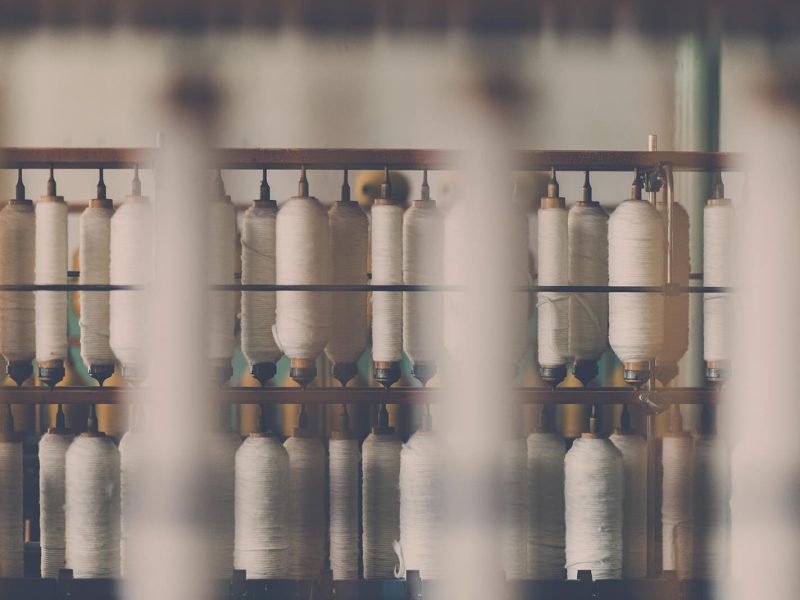
In today’s competitive machining industry, companies are constantly looking for ways to improve efficiency, reduce costs, and stay ahead of the competition. One approach that has gained significant traction is lean manufacturing. Lean manufacturing focuses on eliminating waste, streamlining processes, and maximizing value for customers. Here’s how adopting lean principles can benefit the machining industry:
1. Increased Efficiency
Lean manufacturing emphasizes the importance of streamlining operations by reducing unnecessary steps and focusing on value-adding activities. By analyzing each stage of the machining process, companies can identify bottlenecks, minimize downtime, and ensure that resources are used efficiently. This leads to faster production cycles and improved overall efficiency.
2. Reduced Waste
One of the core principles of lean manufacturing is eliminating waste in all forms—whether it’s overproduction, excess inventory, unnecessary movement, or defects. In the machining industry, reducing waste can lead to significant cost savings. For example, lean practices help reduce scrap material, optimize tool usage, and minimize energy consumption, which ultimately reduces operational costs.
3. Improved Quality Control
Lean manufacturing encourages continuous improvement and a focus on quality at every stage of production. By using techniques like Total Quality Management (TQM) and root cause analysis, manufacturers can identify and address quality issues early in the process, reducing the likelihood of defects and rework. This leads to higher-quality products and greater customer satisfaction.
4. Better Resource Management
Lean practices promote better utilization of both human and machine resources. By organizing workflows, scheduling work more effectively, and reducing machine downtime, manufacturers can maximize their resource output. This means less idle time for machines and employees, leading to higher productivity and cost efficiency.
5. Enhanced Flexibility and Responsiveness
Lean manufacturing systems are designed to be highly adaptable. This flexibility allows machining companies to respond quickly to changes in customer demand or unforeseen challenges, such as material shortages or machine malfunctions. With lean principles in place, manufacturers can improve lead times, deliver faster, and stay more agile in a dynamic market.
6. Improved Employee Engagement
Lean manufacturing encourages a culture of continuous improvement, where all employees are involved in identifying problems and suggesting solutions. This creates a more engaged and motivated workforce, as employees feel valued and empowered to contribute to the company’s success. Increased engagement can lead to higher productivity and lower turnover rates.
Adopting lean manufacturing principles in the machining industry offers numerous benefits, from improved efficiency and reduced waste to better resource management and higher quality. By focusing on continuous improvement, optimizing processes, and creating a culture of collaboration, machining companies can achieve sustainable growth, lower costs, and stay competitive in an ever-evolving industry.