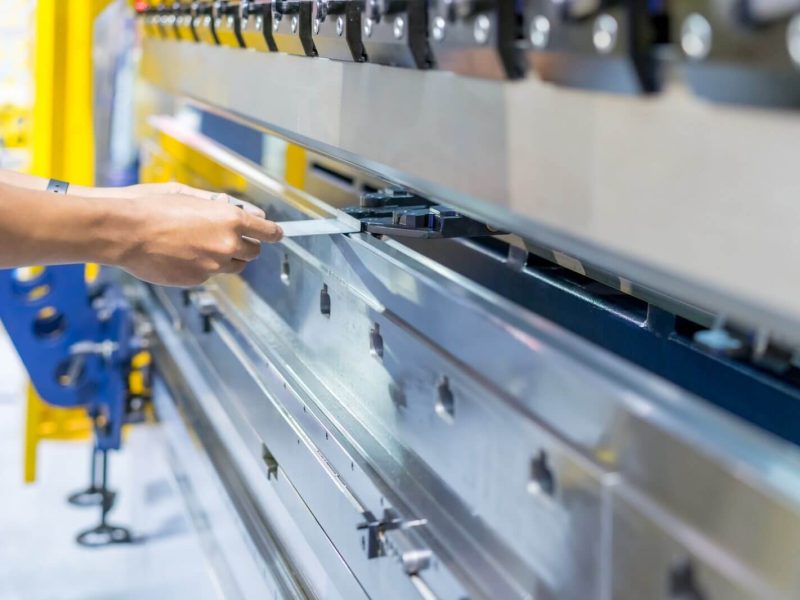
Additive manufacturing, or 3D printing, has become a transformative force in modern machining. While traditional machining methods like CNC milling and turning have long been the backbone of manufacturing, the integration of 3D printing is opening up new possibilities for speed, complexity, and cost-efficiency. Here’s how additive manufacturing is enhancing traditional machining and what it means for the future of production.
Bridging the Gap Between Prototyping and Production
One of the most significant ways additive manufacturing impacts machining is in the prototyping phase. 3D printing allows manufacturers to quickly produce prototype parts with intricate geometries that may be difficult or impossible to achieve with traditional methods. This enables faster iterations and design changes, which can reduce time-to-market and costs.
Enhancing Customization and Flexibility
In traditional machining, creating custom parts often involves significant time and effort, especially for low-volume production runs. Additive manufacturing eliminates many of these challenges by offering a more flexible, on-demand solution. Manufacturers can produce highly customized parts without the need for expensive tooling or molds, making small-batch production and rapid prototyping easier and more cost-effective.
Complementing Traditional Methods
Rather than replacing traditional machining, additive manufacturing often works hand-in-hand with it. For example, 3D printing can be used to create complex or lightweight structures that can then be finished or assembled using traditional machining methods. This hybrid approach leverages the strengths of both techniques, combining the high precision of CNC machining with the versatility and design freedom of 3D printing.
Additionally, additive manufacturing is ideal for producing complex internal geometries—like lattice structures or cooling channels—that are difficult or impossible to machine. By integrating 3D printed components with traditional parts, manufacturers can achieve designs that offer superior performance and efficiency.
Reducing Material Waste and Lead Times
3D printing also plays a role in sustainability and efficiency. Unlike traditional subtractive methods, which remove material to shape a part, additive manufacturing builds parts layer by layer, using only the material needed. This can result in significant material savings, especially when working with expensive or rare materials.
Furthermore, additive manufacturing can drastically reduce lead times. Parts that would normally take days or weeks to machine can be printed in a fraction of the time, allowing manufacturers to meet tight deadlines and reduce inventory.
The combination of additive manufacturing and traditional machining is reshaping the future of production. By harnessing the strengths of both technologies, manufacturers can achieve greater flexibility, reduce material waste, and produce more complex, customized components faster and more efficiently. As both techniques continue to evolve, the line between 3D printing and traditional machining will blur even further, unlocking new possibilities for innovation and efficiency in manufacturing.